반도체(디엔에프)와 전기전자(비나텍) 섹터의 강소 기업만 소재·부품·장비(소부장) 국산화에 기여하는 건 아니다. 소부장 기술 독립 시도는 제조업의 다양한 분야에서 동시다발적으로 이뤄지고 있다. ‘이코노미조선’이 중소벤처기업부 추천을 받아 국산화 우수 사례 가운데 일부를 모았다.
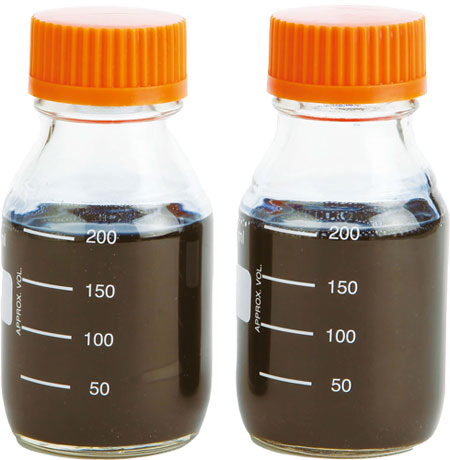
기초화학 | 에버켐텍
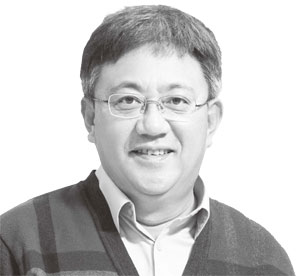
코팅제 등의 화학물질을 전문적으로 만드는 에버켐텍은 일본의 소부장 수출 규제 이슈가 터진 2019년 가장 주목받은 기업 중 한 곳이다. 이 회사가 2019년 개발에 성공한 식품 포장재용 친환경 코팅제 덕분이다.
통상 식품 포장재에는 음식물의 부패를 막기 위해 산소 차단 기능을 넣는다. 이전까지는 일본산 소재인 에틸렌 비닐 알코올(EVOH)이 유일한 산소 차단 물질이었다. 에버켐텍은 유청 단백질을 이용해 EVOH를 대신하는 친환경 코팅제를 만들었다.
에버켐텍은 앞서 2008년에도 일본 기업이 독점하던 디스플레이용 고기능성 대전 방지 코팅제를 국산화해 LG화학·SKC 등 국내 디스플레이 업체에 공급한 바 있다. 디스플레이용 고기능성 대전 방..
이코노미조선 멤버십 기사입니다
커버스토리를 제외한 모든 이코노미조선 기사는
발행일자 기준 차주 월요일 낮 12시에
무료로 공개됩니다.
발행일자 기준 차주 월요일 낮 12시에
무료로 공개됩니다.
멤버십 회원이신가요? 로그인