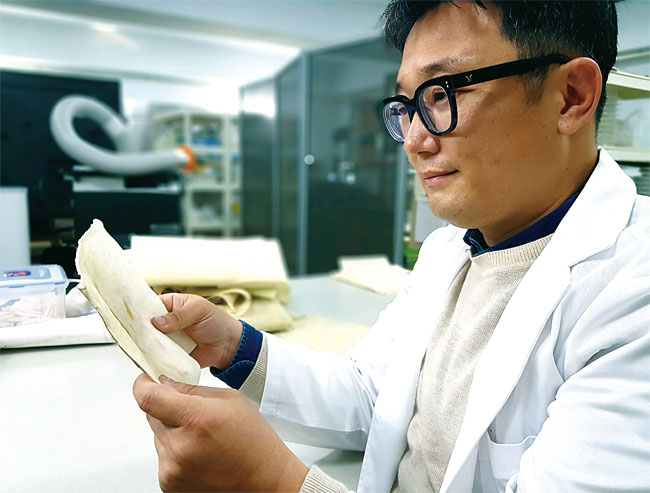
12월 3일 경기도 군포역 인근의 한 빌딩. 버섯 균사체를 이용해 인조가죽을 생산하는 농업 관련 스타트업 ‘마이셀’을 찾았다. 회사 내부는 일반 바이오 기업 실험실과 다를 바 없었다. 연구실 사방의 선반에는 다양한 실험 장비와 버섯 균사체를 키우는 용기가 놓여 있었다.
마이셀은 버섯 균사체를 활용해 인조가죽을 만든다. 기존 합성피혁과 달리 버섯 균사체로 만든 가죽은 천연가죽과 구분이 되지 않았다. 손으로 만져도 천연가죽처럼 느껴졌고, 찢어지지 않을 정도로 질겼다. 사성진(42) 마이셀 대표는 “소재가 늘어나는 것을 버티는 정도인 인장강도나 소재가 찢어지는 정도를 의미하는 인열강도 실험에서 천연가죽에 밀리지 않았다”고 했다.
마이셀은 현대자동차 직원 3명이 회사로부터 15억원을 지원받아 시작한 일종의 사내 스타트업이다. 아직 분사하지 않아 3명 모두 현재는 현대차 소속이다. 이들이 다소 낯선 개념의 인조가죽 개발에 나선 이유가 궁금했다.
버섯 균사체를 소재로 활용하는 인조가죽은 세계 최초인가.
“세계 최초는 아니다. 2010년 마이코웍스라는 회사가 버섯 균사체를 가공한 가죽을 개발했다. 앞서 2007년에는 미국의 에코베이트가 버섯 균사체로 스티로폼을 대체할 수 있는 포장재를 만들기도 했다.”
먼저 사업에 나선 기업이 있는데, 특허에는 문제가 없나.
“버섯 균사체를 활용해 인조가죽 등의 소재를 생산하는 건 범용 기술로 인정받고 있다. 관건은 ‘어떻게 버섯 균사체를 빠르게, 원하는 면적으로 키우는가’이다. 이는 일종의 생산 노하우 경쟁으로 보면 된다. 예컨대 누에를 키워 비단을 생산하는 일은 많은 사람이 할 수 있다. 중요한 것은 누가 건강한 누에를 잘 키워 질 좋은 비단을 생산할 수 있느냐다. 버섯 균사체도 마찬가지다.”
사업을 시작하게 된 배경은.
“프랑스 도로교통안전국 산하 연구소에서 일할 때 요리학교 다니는 한국인 친구를 만났다. 그가 한국 버섯을 활용한 요리로 요리 경연대회에서 1위를 차지한 적이 있다. 그때 한국 농부들이 멋진 기술로 최고 품질의 버섯을 재배한다는 사실을 알게 됐고, 이후 버섯의 다양한 쓰임새에 관심을 두고 사업 아이템을 고민하기 시작했다. 어느 날 버섯 재배 농장에서 버섯 뿌리에 해당하는 균사체가 가득한 배지를 버린다는 사실을 알게 됐다. 아깝다는 생각이 들어 재활용 방법을 고민하는 와중에 미국에서 버섯 균사체로 포장재와 가죽을 만든다는 정보를 접했다. 특허에도 문제가 없다는 사실을 파악한 뒤 적용 기술 개발에 착수했다.”
왜 하필 인조가죽이었나.
“차량에 쓰는 천연가죽은 가공 과정에서 엄청난 양의 물을 소비하고 환경오염을 유발한다. 환경 규제가 강력하지 않았던 과거에는 가죽 가공 공장 주변 하천이 늘 썩은 상태였다. 합성피혁은 천연가죽 특유의 질감과 고급스러움을 그대로 구현하지 못할 뿐 아니라 자동차를 폐차할 때 심각한 환경오염을 유발할 수 있다. 우리는 천연 소재인 버섯 균사체를 사용하면 기존 가죽 소재의 문제점을 해결할 수 있다고 판단했다.”
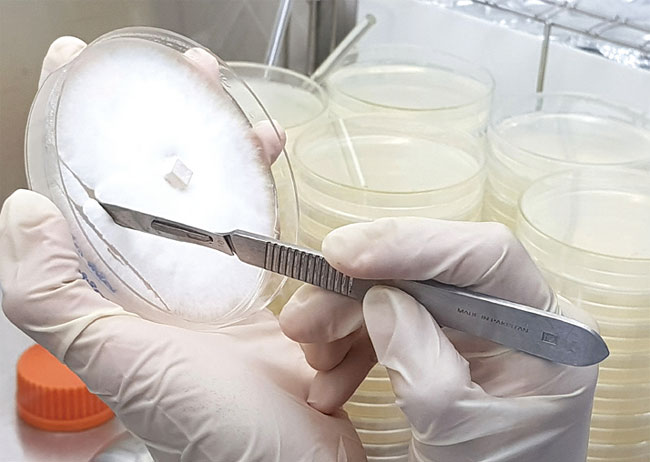
주로 어떤 버섯의 균사체를 이용하는가.
“상황버섯·영지버섯·느타리버섯의 균사체로 가죽을 만든다. 이들 버섯 균사체보다 더 좋은 균사체가 있는지 계속 연구할 계획이다.”
버섯 균사체로 가죽을 만드는 과정에 관해 설명해 달라.
“버섯 균사체를 확보한 뒤 가장 먼저 하는 일은 표백 작업이다. 원재료를 하얗게 표백해야만 염색한 뒤 균일하게 원하는 색을 얻을 수 있다. 이후 균사체에 바이오폴리머를 넣어 강도를 높이는 동시에 부드럽게 만드는 과정을 거친다. 바이오폴리머는 전분이나 펙틴 같은 식물성 고분자 화합물이다. 마지막으로 원하는 색을 입히는 염색·코팅 작업을 하면 인조가죽이 탄생한다.”
천연가죽을 대체하기 위해서는 생산비가 천연가죽보다 저렴해야 할 텐데.
“생산 비용 측면에서 경쟁력이 있다. 소 한 마리의 가죽을 가공하는 비용은 6만8000원쯤이다. 버섯 균사체를 이용해 같은 크기의 가죽을 생산하는 데에는 4만8000원이 든다. 2만원 싸다.”
버섯 균사체 가죽의 또 다른 장점은.
“천연가죽 생산에 주로 쓰이는 소가죽은 가공 단계가 무려 10단계에 달한다. 버섯 균사체 가죽은 공정을 이보다 크게 줄여 생산비를 절감할 수 있다. 폐기물 발생량도 적다. 소가죽을 생산할 때 원피 무게의 30%가 폐기물이다. 게다가 버섯 균사체를 이용한 인조가죽 생산에 필요한 물의 양도 천연가죽의 1%면 충분하다.”
버섯 균사체를 생산하고 남은 폐기물은 버리나.
“우리는 목재 톱밥과 커피 찌꺼기, 배양액 등으로 균사체를 키우는데, 균사체를 수확하고 남아도 버리지 않는다. 목재나 커피 찌꺼기는 퇴비로 만들어 쓸 수 있고, 열압축하면 보드나 타일로 만들 수도 있다. 균사체를 키우고 남은 배양액도 유용하다. 배양액에 체외 다당체인 베타글루칸 등 발효 물질이 들어 있어 화장품이나 의약품 원료로 활용할 수 있다.”
생산비가 저렴하고 친환경적이어도 다양한 용도로 사용할 수 있어야 할 텐데.
“기존 천연가죽과 인조가죽이 쓰이는 곳이라면 버섯 균사체 가죽도 사용 가능하다. 평탄화 과정을 거친 뒤 가죽 엠보 패턴을 넣은 버섯 균사체 가죽은 천연가죽과 비슷한 느낌을 낸다. 패션 디자이너들과 협업해 가방·지갑 등을 만들었는데, 천연가죽 제품과 다르지 않다는 평가를 받았다.”
대체가죽 시장 규모는 얼마나 되나.
“석유화합물을 기본 원료로 하는 합성피혁을 포함한 글로벌 대체가죽 시장은 850억달러(약 87조원)에 달한다. 국내 시장도 어림잡아 4000억원쯤으로 추산한다. 우리는 버섯 균사체 가죽이 기존 합성피혁보다 경제적이고 친환경적이기 때문에 시장 점유율을 빠르게 끌어올릴 것으로 기대한다.”
언제부터 본격적인 생산에 돌입하나.
“내년 1분기에 회사를 현대차에서 스핀오프(spin-off·분사)하고, 2분기부터 원하는 크기의 버섯 균사체를 키우는 실증 과정에 착수한다. 내년 4분기부터는 균사체를 원료로 한 가죽 제품을 본격적으로 생산할 것이다. 늦어도 2021년 말까지 대량 생산 시스템을 구축한 다음 2022년 2분기쯤 자동차 시트용 가죽을 공급한다는 목표를 세웠다. 균사체 배양액을 활용한 화장품도 2021년부터 생산하기 시작해 시장 반응을 살필 계획이다. 인공육 개발에도 관심 있다.”
버섯 균사체도 직접 생산할 것인가.
“직접 생산할 계획은 없다. 앞에서 언급한 대로 한국 농가의 버섯 재배 기술은 세계 최고 수준이다. 균사체 생산은 농가에 맡기는 게 좋다고 생각한다. 우리는 이를 공급받아 가죽으로 가공한 뒤 자동차 회사, 패션 회사 등에 납품하는 데 집중할 것이다.”