
2 테슬라의 첫 번째 공장인 캘리포니아주 프리몬트 공장. 프레스 공장(Stamping), 차체 공장(Body, 주로 패널의 용접·본딩), 도장 공장(Paint), 의장 공장(조립 공장, General Assembly) 등이 거리를 두고 따로 배치돼 있다.
3 테슬라 오스틴 공장은 거대한 단일 공장 내부에 프레스, 차체, 도장, 의장 공장을 한꺼번에 모아 하나의 흐름으로 연결하고 있다. 특히 공장 4층에서 셀을 제조하고, 그 셀을 3층으로 내려 팩을 제조하고, 그 팩을 다시 2층으로 내려 최종 조립하는 형태는, 부품의 이동 거리·시간을 단축하는 데 매우 효과적이다. 사진 테슬라 동영상 캡처
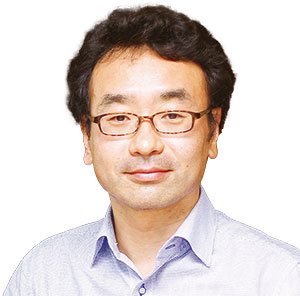
영화 ‘마이너리티 리포트(Minority Report·2002년)’에는 주인공 톰 크루즈가 ‘2054년형 렉서스’를 만드는 공장에서 적에게 쫓기는 장면이 나온다. 공장 안을 살펴보면 특이한 점이 눈에 띈다. 자동차는 조립되고 있는데, 인간 작업자가 보이지 않는다. 자동차 공장은 긴 컨베이어벨트 위에 수백·수천 명의 작업자가 늘어서 조립하는 형태. 작업이 하나라도 중단되면 공정 전체가 멈춰버린다는 특징이 있다. 그 때문에 당시는 현장 노동자 권한이 셌고, 어느 나라에서나 강성 노조의 온상이던 시절이 있었다.
그러나 컨베이어벨트, 조립 노동자로 대변되던 자동차 공장이 바뀌고 있다. 자동차 구조가 내연기관차에서 전기차로 바뀌며 변화의 물결이 거세지고 있다. 미래의 자동차 공장이 어떤 모습일지 알려면, 테슬라가 올해 4월 가동한 텍사스주 오스틴 공장을 살펴봐야 한다. 오스틴 공장의 생산 혁신을 세 가지로 분석했다.
1│‘쇳물에서 내연기관차까지’ 100년 전 포드 시스템, ‘배터리 셀부터 전기차까지’ 테슬라의 완전체 일관생산
테슬라 오스틴 공장의 경쟁력은 완전에 가까운 일관생산에 있다. 셀(배터리의 기본 단위)부터 팩(셀을 묶어 전기차 한 대 분 배터리로 만든 것), 차체·도장·조립까지, 전기차 제조에 필요한 핵심 공정을 한 공장에서 완료하는 것이다.
일관생산은 ‘물건을 운반하는 데서 오는 낭비’를 최소화할 수 있어, 생산 속도·비용 면에 많은 이점이 있다. 기존의 전기차 생산에서는 배터리 셀은 물론 수많은 부품이 공급 업체 공장에서 만들어진 뒤 완성차 회사 조립 공장으로 옮겨졌다.
이는 100여 년 전 헨리 포드가 내연기관 차의 일관생산을 완성한 것을 연상케도 한다. 당시 포드는 제철(製鐵)부터 엔진·변속기 등 차량 핵심 부품 제조까지 하나의 생산 시설 내에서 끝내는 내연기관차의 일관생산을 완성해 ‘자동차 왕’이 됐다.
오스틴 공장에서 만들어지는 첫 차종인 모델Y에는 신형 원통형 셀 ‘4680’이 탑재된다. 지름이 기존 제품의 2배, 용량이 5배다. 대형화에 의한 부품 수 삭감 등을 통해, 장기적으로는 배터리 용량당 생산비를 2020년 대비 반값 이하로 만드는 것(56% 삭감)을 목표로 하고 있다.
원래 자동차 공장은 단층 혹은 2층이 대부분이지만 오스틴 공장은 4층 구조로 돼 있다. 4680 배터리 셀이 4층에서 생산된 뒤 바닥을 통과해 3층으로 떨어지고, 3층에서는 셀을 받아 팩으로 조립한다. 이후 완성된 팩은 3층에 대기해 있다가 2층에 있는 완성차 조립 공정에 맞춰 아래로 내려간다. 일관생산, 이전 단계의 무거운 부품을 자중(自重)을 활용해 옮기는 아이디어 등은 원가를 낮출 뿐 아니라, 공장 가동에 드는 에너지를 줄여줘 지속 가능한 생산에도 유리하다.
게다가 오스틴 공장은 하나의 큰 공장 안에 프레스(stamping), 차체(body, 주로 패널의 용접·접착), 도장(paint) 그리고 의장(조립, general assembly)은 물론 배터리 공장까지 모아 놓았다. 반면 테슬라의 첫 번째 완성차 생산 거점인 캘리포니아주 프리몬트 공장은 프레스·차체·도장·의장이 각각 따로다. 배터리는 네바다주 공장에서 만들어 프리몬트까지 운반해야 한다. 대부분의 기존 자동차 공장도 사정은 마찬가지다.

2 오스틴 공장에서 생산되는 모델Y의 언더보디(하부 차체)는 앞쪽을 하나의 주조물, 뒤쪽을 하나의 주조물로 만든 뒤, 중앙은 배터리 자체가 구조물 역할을 하는 식이다. 통상적으로 자동차는 수백 개의 금속 패널을 이어붙여 언더보디를 만들어내는데, 최신 모델Y는 단 세 개의 구조물로 단순화된다. 사진 The Tesla Space 유튜브 캡처
2│포드가 만들어낸 컨베이어 시스템의 종말? 생산 유연성 극대화한 AGV 방식으로
오스틴 공장이 기존 자동차 회사와 다른 또 하나는 조립 라인이다. 차량이 컨베이어가 아니라 AGV(Automated Guided Vehicle·무인운반차량) 위에 올려져 라인을 흐른다. 컨베이어는 결함이 발견될 경우 라인 전체를 멈춰야 하지만, AGV는 결함 있는 차량만 라인 밖으로 빼내면 된다. AGV는 사실상 자율주행 로봇이나 다름없다. 여러 대의 AGV가 연계해 서로 거리를 제어하며 동기화해 움직일 수 있다.
컨베이어 시스템은 100여 년 전 포드가 자동차에 접목한 이후 대량생산의 상식이 됐다. 테슬라가 100년간 지속된 상식을 깬 것이다. 기존 업체 공장에서도 부품 운반이나 특정 수요용 소량생산에 AGV를 활용하긴 하지만, 대량생산 차량 전체를 AGV 위에 올린 사례는 테슬라가 사실상 처음이다.
차량을 AGV에 올려 조립하는 방식은 생산 유연성 향상에 유리하다. 생산량 증감, 차종 배분 등이 컨베이어 방식보다 빠르고 자유롭다. 신차 도입 때도 라인 변경을 최소화할 수 있다. 테슬라 오스틴 공장은 라인 재구축 비용이나 공사 기간을 기존 자동차 공장 대비 10분의 1 이하로 억제할 수 있을 것으로 추정된다.
3│자동차뿐 아니라, 공장 시스템도 무선 업데이트, 디지털트윈 기술의 부상
테슬라 오스틴 공장은 실제 생산에 들어가기 전에 컴퓨터상에서 생산 과정을 재현하는 ‘디지털트윈 기술’과 밀접하게 연결돼 있다. 디지털트윈 기술을 사용함으로써 차량 종류, 생산 속도 등을 바꿀 경우의 영향을 미리 점검할 수 있다. 투자 비용은 물론 양산까지의 소요 시간을 크게 줄이고 품질 안정화도 빨리 이룰 수 있다.
테슬라 방식이 훌륭한 것은 문제점을 발견했을 때, 대부분의 문제를 AGV나 다른 생산 설비의 OTA(Over The Air·무선 업데이트)를 통해 곧바로 해결할 수 있다는 것이다. 실시간 혹은 몇 시간이면 대부분의 문제 해결이 가능하고, 생산 레이아웃 전체를 변경하는 대공사도 하루면 충분할 것으로 보인다.
테슬라 오스틴 공장은 연면적이 92만㎡(28만 평)로 펜타곤의 세 배에 달할 만큼 크다. 초기 투자는 10억달러(약 1조3000억원)였지만 장기적으로 100억달러(약 13조원) 이상 투입된다. 완성차 공장 투자는 1조원대에서 끝나는 게 일반적. 테슬라가 단일 공장에 12조원 이상 투자한다는 것은 이 공장이 미래에 더 많은 일을 하게 될 것이라는 것을 짐작케 한다.
물론 ‘테슬라 생산 시스템’이 만능은 아니다. 공장 수를 제한하면서 단일 공장의 생산 스피드를 극도로 높이는 방식이 효율적으로 보이긴 하나, 지난 3월 중국 팬데믹(pan-demic·감염병 대유행)에 따른 상하이 공장 셧다운에서 봤듯이 국지적 리스크에 취약할 수 있다. 또 테슬라의 급격한 기술·공정 변경은 결함 발생 가능성을 키울 우려가 있다. 치명적인 제품 결함이 나올 경우, 회사 전체가 흔들리는 큰 위기에 빠질 수도 있다.